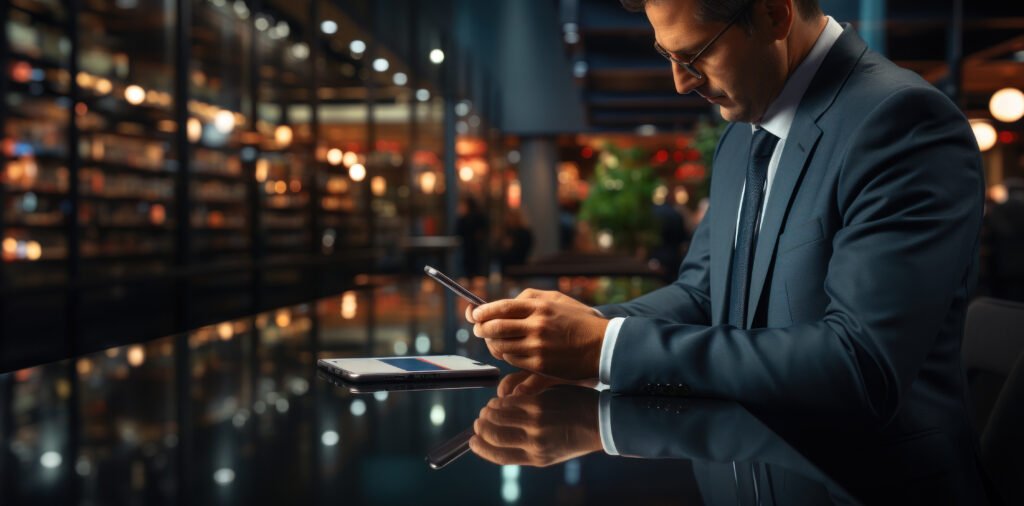
Predictive Maintenance (PdM) is revolutionizing the way businesses maintain equipment, delivering cost savings, increased efficiency, and reduced downtime. This advanced strategy uses data-driven tools to predict when maintenance is needed, preventing unexpected failures and optimizing performance.
Predictive Maintenance is a proactive approach to equipment management. It involves using sensors, data analysis, and machine learning to monitor equipment in real-time. By detecting anomalies and predicting potential issues, businesses can perform maintenance before problems arise.
Industry 4.0 marks the fourth wave of industrial transformation, building on the digital technology and automation introduced in the previous era, the third industrial revolution. While the earlier wave brought greater efficiency, it also created challenges like data security issues, complex maintenance, and higher costs.
Industry 4.0 tackles these challenges with advanced technologies such as the Internet of Things (IoT), cloud computing, big data, machine learning, artificial intelligence, and augmented reality. These innovations are transforming maintenance strategies, making systems more reliable, reducing costs, improving safety, and minimizing unplanned downtime.
The versatility of Predictive Maintenance means it can be adapted to almost any industry. However, for the best results, businesses should focus on areas where predictive insights can deliver the most value. While the tools and techniques may be similar, each application is tailored to the specific needs and processes of the business. Let’s explore its impact across industries.
In manufacturing, Predictive Maintenance is a game-changer, particularly for CNC machines used in high-precision tasks like cutting and drilling. Sensors track data like vibrations and operational patterns, while AI predicts potential breakdowns. This proactive approach keeps production running smoothly, minimizing costly downtime.
For the automotive sector, Predictive Maintenance goes beyond production lines. Fleet management systems analyze data from vehicles—such as engine performance, fuel usage, and driver behavior to predict maintenance needs. This ensures fleets run efficiently, reducing breakdowns and maintenance costs.
In healthcare, downtime in medical equipment like MRI machines can be critical. Predictive Maintenance monitors these devices through IoT sensors, tracking performance and usage data. This ensures timely maintenance, reducing downtime and improving the availability of life-saving equipment.
Predictive Maintenance is widely used in renewable energy, especially for wind turbines. AI systems analyze data on vibrations, rotor speeds, and temperatures to predict when maintenance is needed. This is particularly valuable since wind farms are often remote and difficult to access quickly.
In the oil and gas sector, equipment failures can disrupt production and pose environmental risks. Predictive Maintenance uses IoT sensors to monitor pumps, valves, and compressors, helping operators address issues before they escalate. This enhances safety and reduces downtime.
Aircraft maintenance is crucial for safety and efficiency. Predictive Maintenance analyzes engine and sensor data to predict when components might fail. This allows for timely repairs, minimizing aircraft downtime and improving passenger safety.
For telecom companies, Predictive Maintenance ensures stable network performance. By monitoring routers, switches, and other hardware, these systems predict potential failures, preventing outages and maintaining consistent service quality.
Farm equipment is vital during planting and harvesting seasons. Predictive Maintenance uses IoT sensors and environmental data to monitor equipment and predict maintenance needs. This reduces downtime, boosting productivity and ensuring timely operations.
From keeping airplanes safe to ensuring medical equipment is ready to save lives, Predictive Maintenance is transforming industries. As technology evolves, its applications will only grow, helping businesses optimize operations and achieve their goals. Organizations that fail to embrace predictive maintenance risk falling behind and missing out on a critical competitive edge.
Sign up for my newsletter to get latest updates. Do not worry, we will never spam you.